在 PCBA 设计中,普通整流二极管作为电力转换与整流电路的核心元件,其设计合理性直接影响整机可靠性。但实际工程中,因设计细节疏漏导致的二极管失效案例屡见不鲜。作为 FAE,结合现场调试经验,以下为普通整流二极管 PCBA 设计中的常见问题及应对策略。
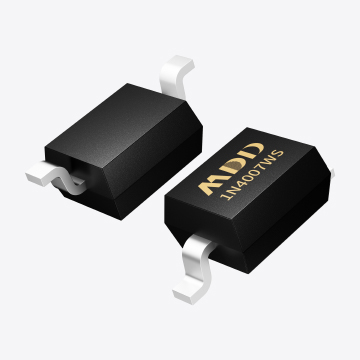
散热设计缺陷是最易被忽视的关键问题。整流二极管导通时的功耗会转化为热量,若散热路径设计不合理,结温会快速攀升至超过额定值。例如某工业电源项目中,工程师选用 10A 整流二极管时仅保留 2mm² 的铜皮散热,导致连续工作 30 分钟后二极管结温达 150℃(额定结温 125℃),最终引发热击穿。解决这一问题需从三方面入手:一是根据二极管额定功耗计算最小散热铜皮面积(通常每 1W 功耗需 8-10mm² 铜皮);二是在铜皮下方增加散热过孔(建议 φ0.3mm 过孔,间距 2mm),将热量传导至 PCB 背面;三是大功率场景下需搭配散热片,通过导热硅胶降低接触热阻。
布局不合理引发的寄生参数干扰同样不容忽视。在高频整流电路中,二极管引线过长会引入寄生电感,反向恢复期间电感与二极管结电容形成 LC 振荡,产生的尖峰电压可能超过反向耐压值。某适配器项目中,整流二极管与滤波电容间距达 50mm,实测反向尖峰电压达 600V(二极管耐压 400V),导致批量性击穿。优化布局的核心是缩短高频路径:二极管应紧邻整流桥或负载端,引线长度控制在 5mm 以内;同时将滤波电容就近布置,形成 “二极管 - 电容” 的紧凑回路,减少寄生电感。
焊接工艺问题常导致隐性失效。焊盘设计不当是主要诱因,例如将 DO-214AC 封装的二极管焊盘长度设计为 5mm(标准应为 6.5±0.5mm),会导致焊接时焊锡无法充分浸润,形成虚焊。回流焊温度曲线失控同样危险,温度过高(超过 260℃)会导致二极管芯片氧化,温度过低则会出现冷焊。解决方案包括:严格按照封装手册设计焊盘(如 SMA 封装焊盘宽度应与引脚宽度一致,误差≤0.2mm);回流焊峰值温度控制在 240±5℃,保温时间 30-60 秒;波峰焊时确保引脚完全浸入焊锡,浸锡深度为引脚长度的 1/2-2/3。
反向耐压余量不足易引发瞬时击穿。实际应用中,电网波动或感性负载断开时会产生反向浪涌电压,若二极管选型时未预留足够余量,极易发生击穿。例如 220V 交流整流电路中,峰值电压约 311V,若选用 300V 耐压的二极管,在电网电压波动至 240V 时,反向电压会达到 340V,超过额定值。正确的选型原则是:反向耐压值应为实际最大反向电压的 1.5-2 倍,同时在电路中增加 RC 吸收回路(电阻 100Ω-1kΩ,电容 0.1-0.47μF),抑制浪涌尖峰。
静电防护缺失会导致二极管隐性损伤。虽然整流二极管的静电敏感性低于 MOS 管,但在干燥环境下,人体静电(可达 30kV)仍可能击穿其氧化层。某消费电子产线因未采取防静电措施,导致整流二极管在出厂测试中合格率达 98%,但用户使用 3 个月后失效比例升至 15%。预防措施包括:PCB 设计时在二极管引脚附近增加接地保护环(宽度≥0.5mm);装配过程中使用防静电手环、工作台;存储时采用防静电包装。
总之
普通整流二极管的 PCBA 设计需兼顾散热、布局、工艺、选型与防护五大维度。通过精细化设计规避常见问题,可显著提升电路可靠性,降低后期维护成本。作为 FAE,需在设计阶段提前介入,结合应用场景提供针对性方案,才能充分发挥整流二极管的性能优势。